Project:
Contact:
via mail ✉
Object:
Type:
window shading element
Location:
Eindhoven [satellite]
Country:
The Netherlands
Architect:
Neutelings Riedijk Architects 🔗, Rotterdam
Materials:
3d-print of concrete
Published:
Beton Bauteile 2025
Pages:
152 -155
Content:
Gedruckte Sandformfassaden, TU Eindhoven/NL
Sandkasten für Roboter
An der TU Eindhoven wurde ein nachhaltiges Konzept zum 3D- Druck von Betonbauteilen auf sphärisch gekrümmten Untergründen entwickelt und ein daraus resultierender Prototyp eines Fassadenverschattungssystems aus gedruckten Betonelementen vorgestellt.
[no english version available]
In der Regel sind die Grundflächen, auf denen ein 3D- Betondruck entsteht, horizontal ausgerichtet und planar. Aber dem muss ja nicht so sein: Will man nun bei einem gedruckten Betonelement eine anders geartete Standfläche erhalten, würde man für gewöhnlich zunächst eine entsprechend geformte Grundplatte, etwa aus Holz oder aus Kunststoff, produzieren. Auf dieser würde man dann den Betondruck ausführen. Doch mit Blick auf die Kosten und auch die Nachhaltigkeit ist dieses Vorgehen von großem Nachteil, denn nach jeder Drucksession fällt dieses individuelle Untergrundelement als Abfall an.
Drucken mit Sandformen
Vor diesem Hintergrund wurde am Lehrstuhl für architektonisches Design und Ingenieurbau an der TU Eindhoven (TU/e) ein Verfahren entwickelt, bei dem anstatt mit einer harten, individuell angefertigten Bodenplatte mit geringfügig verdichtetem Sand in einer flachen Kiste gearbeitet wird. Wissenschaftlich verantwortlich waren zu gleichen Teilen Prof. Juliette Bekkering und Prof. Cristina Nan, die beide an dem Lehrstuhl tätig sind.
Vor dem eigentlichen Betondruck wird das flache Sandvolumen mit einem Spachtel, der an einem Roboterarm montiert ist, präzise in Form gebracht. Tatsächlich handelt es sich um denselben Roboter, der anschließend auch den Betondruck ausführt. Hier wird zwischenzeitlich nur das Glättwerkzeug gegen eine Druckdüse ausgetauscht. Nach dem Aushärten des Betondrucks hebt man diesen vorsichtig aus seinem Sandbett, welches anschließend durchgesiebt wird und sofort wieder für den nächsten Druck verwendet werden kann.
Im Vorfeld wurden umfangreiche Versuche gefahren, um herauszufinden, welches dreidimensionale Relief eine lose Sandstruktur überhaupt für einen stabilen 3D- Druck einnehmen kann. Untersucht wurden dabei sowohl die Frage nach einer maximalen Steilheit der Sanderhebungen als auch die Frage nach der Schärfe ihrer Grate, bevor sie während eines Drucks kollabieren. Gearbeitet wurde aber nicht mit angefeuchtetem Sand. Prof. Nan betont, dass vor der TU/e andere mit Sand-schalungen operierten. Sie erinnert an Iannis Xenakis und Le Corbusier, die 1958 auf der Brüsseler Weltaustellung den Philips Pavillon aus Sandformen schufen.
Auch in der klassischen Moderne hatten Architekten immer wieder mit Sandschalungen für ihre skulpturalen Betonvolumina gearbeitet. Auch aktuell arbeiten verschiedene Forschungsinstitute und Unternehmen an Verfahren zur Herstellung von Betonkörpern unter Verwendung von Sandformen und -schalungen. Stellvertretend sei hier der Marinaressa Coral Tree genannt, der vom ILEK in Stuttgart im vergangenen Jahr auf der Biennale von Venedig gezeigt wurde. Wir hatten in der vergangenen Ausgabe dieses Jahrbuchs ausführlich darüber berichtet.
Vor diesem Hintergrund wurde am Lehrstuhl für architektonisches Design und Ingenieurbau an der TU Eindhoven (TU/e) ein Verfahren entwickelt, bei dem anstatt mit einer harten, individuell angefertigten Bodenplatte mit geringfügig verdichtetem Sand in einer flachen Kiste gearbeitet wird. Wissenschaftlich verantwortlich waren zu gleichen Teilen Prof. Juliette Bekkering und Prof. Cristina Nan, die beide an dem Lehrstuhl tätig sind.
Vor dem eigentlichen Betondruck wird das flache Sandvolumen mit einem Spachtel, der an einem Roboterarm montiert ist, präzise in Form gebracht. Tatsächlich handelt es sich um denselben Roboter, der anschließend auch den Betondruck ausführt. Hier wird zwischenzeitlich nur das Glättwerkzeug gegen eine Druckdüse ausgetauscht. Nach dem Aushärten des Betondrucks hebt man diesen vorsichtig aus seinem Sandbett, welches anschließend durchgesiebt wird und sofort wieder für den nächsten Druck verwendet werden kann.
Im Vorfeld wurden umfangreiche Versuche gefahren, um herauszufinden, welches dreidimensionale Relief eine lose Sandstruktur überhaupt für einen stabilen 3D- Druck einnehmen kann. Untersucht wurden dabei sowohl die Frage nach einer maximalen Steilheit der Sanderhebungen als auch die Frage nach der Schärfe ihrer Grate, bevor sie während eines Drucks kollabieren. Gearbeitet wurde aber nicht mit angefeuchtetem Sand. Prof. Nan betont, dass vor der TU/e andere mit Sand-schalungen operierten. Sie erinnert an Iannis Xenakis und Le Corbusier, die 1958 auf der Brüsseler Weltaustellung den Philips Pavillon aus Sandformen schufen.
Auch in der klassischen Moderne hatten Architekten immer wieder mit Sandschalungen für ihre skulpturalen Betonvolumina gearbeitet. Auch aktuell arbeiten verschiedene Forschungsinstitute und Unternehmen an Verfahren zur Herstellung von Betonkörpern unter Verwendung von Sandformen und -schalungen. Stellvertretend sei hier der Marinaressa Coral Tree genannt, der vom ILEK in Stuttgart im vergangenen Jahr auf der Biennale von Venedig gezeigt wurde. Wir hatten in der vergangenen Ausgabe dieses Jahrbuchs ausführlich darüber berichtet.
Ästhetik des 3D- Drucks
Vor vielen Jahrzehnten wurde mit dem heutzutage noch geläufigen Marketing- Claim „Beton. Es kommt drauf an, was man draus macht“ Werbung gemacht. Aktuell stört Frau Prof. Bakkering insbesondere die formale Limitierung, die die aktuelle Betondrucktechnik vorgibt und in die sich die Planer in ihren Architekturentwürfen gottergeben fügen. Als Beispiel führt sie die runden Ecken der zahlreichen gedruckten Testbauten an. Sie verweist unter anderem auf das Hous3Druck im deutschen Beckum, das von Mense Korte ingenieure + architekten entworfen wurde und das unter Mitwirkung der Peri GmbH entstand.
Sie argumentiert, dass sich das Druckverfahren schlichtweg nicht eignet, wenn man rechte Winkel bei einem Bau will und man eine andere Lösung finden muss. Letztlich lehnt sie es ab, eine Architektur und deren Ästhetik der Bauweise unterzuordnen. Die Bauart müsse stets der Ästhetik dienen. Aufgrund dieser Prämisse warf sie die Frage auf, welche Details, welche Bauprodukte denn überhaupt für die formalen Möglichkeiten eines Betondruck geeignet seien.
Zusammen mit dem Rotterdamer Architekturbüro Neutelings Riedijk, dessen Naturalis Biodiversity Center in Leiden wir in unserer Ausgabe von 2022 vorstellten, entwickelte ihr Lehrstuhl ein kreisförmiges Verschattungselement, das im Betondruck erstellt und als zweite Wandschicht vor eine Glasfassade gestellt werden könnte. Zusammen mit dem guten Speichervermögen des Betons könnte ein solches Bauwerk vor zu viel Sonneneinstrahlung in passiver Weise gut geschützt werden. Der individuelle 3D- Druck ermöglicht hier bei jedem einzelnen Schattensegment eine engmaschige Bewertung, wie viel Durchsicht (und damit auch Sonneneintrag) man an welcher Stelle der abgeschatteten Gesamtfläche haben möchte. So könnte es Positionen geben an denen eine kleinflächige Durchsicht günstig wäre, etwa um eine bestimmte Blickbeziehung herzustellen. Auf der anderen Seite könnte in den oberen Fassadenbereichen die Verschattung durchaus dichter ausfallen, weil dort niemand direkt nach außen schaut. Auf den hier gezeigten Renderings erkennt man gut die wechselnde Dichtheit der Verschattungselemente.
Vor vielen Jahrzehnten wurde mit dem heutzutage noch geläufigen Marketing- Claim „Beton. Es kommt drauf an, was man draus macht“ Werbung gemacht. Aktuell stört Frau Prof. Bakkering insbesondere die formale Limitierung, die die aktuelle Betondrucktechnik vorgibt und in die sich die Planer in ihren Architekturentwürfen gottergeben fügen. Als Beispiel führt sie die runden Ecken der zahlreichen gedruckten Testbauten an. Sie verweist unter anderem auf das Hous3Druck im deutschen Beckum, das von Mense Korte ingenieure + architekten entworfen wurde und das unter Mitwirkung der Peri GmbH entstand.
Sie argumentiert, dass sich das Druckverfahren schlichtweg nicht eignet, wenn man rechte Winkel bei einem Bau will und man eine andere Lösung finden muss. Letztlich lehnt sie es ab, eine Architektur und deren Ästhetik der Bauweise unterzuordnen. Die Bauart müsse stets der Ästhetik dienen. Aufgrund dieser Prämisse warf sie die Frage auf, welche Details, welche Bauprodukte denn überhaupt für die formalen Möglichkeiten eines Betondruck geeignet seien.
Zusammen mit dem Rotterdamer Architekturbüro Neutelings Riedijk, dessen Naturalis Biodiversity Center in Leiden wir in unserer Ausgabe von 2022 vorstellten, entwickelte ihr Lehrstuhl ein kreisförmiges Verschattungselement, das im Betondruck erstellt und als zweite Wandschicht vor eine Glasfassade gestellt werden könnte. Zusammen mit dem guten Speichervermögen des Betons könnte ein solches Bauwerk vor zu viel Sonneneinstrahlung in passiver Weise gut geschützt werden. Der individuelle 3D- Druck ermöglicht hier bei jedem einzelnen Schattensegment eine engmaschige Bewertung, wie viel Durchsicht (und damit auch Sonneneintrag) man an welcher Stelle der abgeschatteten Gesamtfläche haben möchte. So könnte es Positionen geben an denen eine kleinflächige Durchsicht günstig wäre, etwa um eine bestimmte Blickbeziehung herzustellen. Auf der anderen Seite könnte in den oberen Fassadenbereichen die Verschattung durchaus dichter ausfallen, weil dort niemand direkt nach außen schaut. Auf den hier gezeigten Renderings erkennt man gut die wechselnde Dichtheit der Verschattungselemente.
Demonstratoren als Ideen- Synthese
Bis zum Sommer 2024 wurden vier kleinflächige Demonstratoren erstellt. Produziert wurden sie von dem Eindhovener Betondruckdienstleister Vertico, über den wir auch an anderer Stelle in diesem Buch noch einmal berichten im Zusammenhang mit dem Hexastone Pavillon der TH Lübeck. Die Verschattungsdemonstratoren verbinden das Konzept des Sandformdrucks mit den geschilderten ästhetischen Überlegungen. So entstanden diese Testkörper auf Sandformen, bei denen der Untergrund sphärisch gekrümmt war. Im Grunde kann man sich die ausgeführten Betonelemente – Brillengläsern nicht unähnlich – als einseitig gewölbte Linsen vorstellen. Die neuen Bauelemente verortet Volker Ruitinga, Geschäftsführer von vertico, in einer Größe knapp unterhalb von 120 x 80 cm, der Größe einer Europalette. Es hat sich in der Vergangenheit gezeigt, dass dies logistisch ein sehr effektives Vorgehen ist.
Eine technische Herausforderung war allerdings bei Druckbeginn das Wegrollen der Betonwulst unmittelbar nach Düsenaustritt auf einem stark geneigten Untergrund zu vermeiden. Eine praktikable Lösung fand sich in einem leichten Eindrücken des Betons in den Sand. Natürlich verfügt kein Roboter über eine solche taktile Fähigkeit wie ein Mensch. Das Vorgehen ist hier ein rein mathematisches: Eine Betonwulst ist soundsoviel Millimeter hoch, und für ein präzises Aufbringen muss die Düse entsprechend eine bestimmte Höhe über dem Untergrund haben. Will man die Betonmasse nun etwas eindrücken, legt man diesen Höhenwert etwas geringer an als eigentlich erforderlich. Da der sandige Untergrund nachgibt, ist dies ohne eine Wulstverformung möglich. Bei einem harten Untergrund entstünde hingegen ein Materialstau an der Austrittsdüse.
Mit dem 3D- Druck wurde eine offen amorphe Gitterstruktur als Schattenelement geschaffen. Bewusst wurden die Druckwülste mitunter so eng nebeneinanderher geführt, dass sich das Material miteinander verband und sich nach dem Aushärten nunmehr gegenseitig statisch verstärkt.
Bis zum Sommer 2024 wurden vier kleinflächige Demonstratoren erstellt. Produziert wurden sie von dem Eindhovener Betondruckdienstleister Vertico, über den wir auch an anderer Stelle in diesem Buch noch einmal berichten im Zusammenhang mit dem Hexastone Pavillon der TH Lübeck. Die Verschattungsdemonstratoren verbinden das Konzept des Sandformdrucks mit den geschilderten ästhetischen Überlegungen. So entstanden diese Testkörper auf Sandformen, bei denen der Untergrund sphärisch gekrümmt war. Im Grunde kann man sich die ausgeführten Betonelemente – Brillengläsern nicht unähnlich – als einseitig gewölbte Linsen vorstellen. Die neuen Bauelemente verortet Volker Ruitinga, Geschäftsführer von vertico, in einer Größe knapp unterhalb von 120 x 80 cm, der Größe einer Europalette. Es hat sich in der Vergangenheit gezeigt, dass dies logistisch ein sehr effektives Vorgehen ist.
Eine technische Herausforderung war allerdings bei Druckbeginn das Wegrollen der Betonwulst unmittelbar nach Düsenaustritt auf einem stark geneigten Untergrund zu vermeiden. Eine praktikable Lösung fand sich in einem leichten Eindrücken des Betons in den Sand. Natürlich verfügt kein Roboter über eine solche taktile Fähigkeit wie ein Mensch. Das Vorgehen ist hier ein rein mathematisches: Eine Betonwulst ist soundsoviel Millimeter hoch, und für ein präzises Aufbringen muss die Düse entsprechend eine bestimmte Höhe über dem Untergrund haben. Will man die Betonmasse nun etwas eindrücken, legt man diesen Höhenwert etwas geringer an als eigentlich erforderlich. Da der sandige Untergrund nachgibt, ist dies ohne eine Wulstverformung möglich. Bei einem harten Untergrund entstünde hingegen ein Materialstau an der Austrittsdüse.
Mit dem 3D- Druck wurde eine offen amorphe Gitterstruktur als Schattenelement geschaffen. Bewusst wurden die Druckwülste mitunter so eng nebeneinanderher geführt, dass sich das Material miteinander verband und sich nach dem Aushärten nunmehr gegenseitig statisch verstärkt.
Testfassade in Planung
Natürlich sind Neutelings Riedijk, die TU/e und auch Vertico sehr daran interessiert, zeitnah eine größere Fassadenfläche eines Gebäudes mit diesem Detail zu bestücken. Tatsächlich gibt es derzeit entsprechende ernstzunehmende Gespräche mit potenziellen Bauherren. Für konkrete Aussagen, wie und wo eine solche Fassade real entstehen könnte, ist es aber derzeit noch viel zu früh.
Robert Mehl, Aachen
http://www.bft-international.com
Natürlich sind Neutelings Riedijk, die TU/e und auch Vertico sehr daran interessiert, zeitnah eine größere Fassadenfläche eines Gebäudes mit diesem Detail zu bestücken. Tatsächlich gibt es derzeit entsprechende ernstzunehmende Gespräche mit potenziellen Bauherren. Für konkrete Aussagen, wie und wo eine solche Fassade real entstehen könnte, ist es aber derzeit noch viel zu früh.
Robert Mehl, Aachen
http://www.bft-international.com
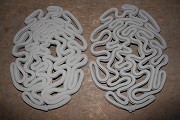
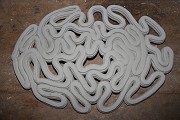